Managing a supply chain is like assembling a complex puzzle. Without proper consideration, pieces that should fit seamlessly together won’t connect properly. This can have an impact on the entire network of your supply chain. Balancing sourcing, production, distribution, and delivery is complex. To enhance control, businesses use vertical integration – owning and controlling various supply chain stages. This reduces reliance on external suppliers, boosting resilience. It lets companies manage schedules, allocate resources, and maintain consistent quality. This proactive approach aids in handling disruptions and ensuring customer satisfaction even during challenges. Research indicates that companies that adopt a vertical supply chain approach and collaborate with a single provider throughout the entire process can reduce their product development cycle costs by an average of 10-20%. But why and how? Let’s discuss. This article will cover:
- Navigating Supply Chain Complexities
- Why are Supply Chains Vulnerable?
- What is a Lean Supply Chain & Is it for your Business?
- What is an Agile Supply Chain & Is it for your Business?
- Is there a Third Option?
- All-In-One Partner and Cost Optimization?
- Challenges with Supply Chain and Data Security
- Potential Market for Mass Personalization
- An All-In-One Supply Chain Resilience and Customization
Navigating Supply Chain Complexities
As discussed earlier, it helps to imagine the supply chain as a challenging puzzle, where numerous intricately shaped pieces seamlessly fit together to ensure products reach consumers’ hands. At the heart of this puzzle are various entities, each representing a distinct stage crucial for delivering goods to the end-users.
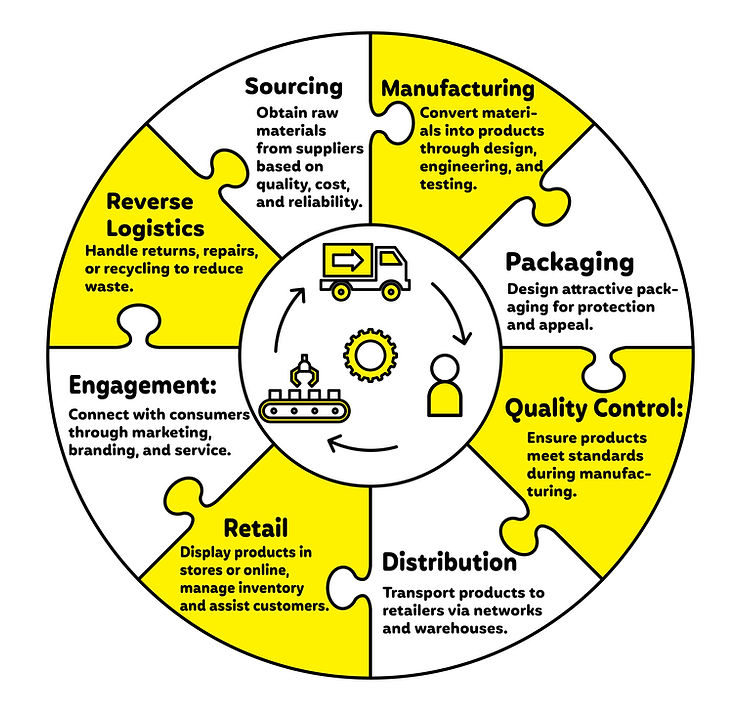
As shown above, a single misplaced puzzle piece can have a big impact on the whole supply chain process. This can make your supply chain weaker, which then affects your cost, how well things work, and even your business reputation.
So Why are Supply Chains Vulnerable?
In this complex network, unexpected disruptions can occur. Natural disasters, economic changes, or global events like the COVID-19 pandemic can disrupt the flow of goods, causing delays and financial stress for businesses. For example, during the pandemic, 77% of US consumers made changes to their shopping behavior, such as switching stores or brands. The primary driver behind these changes was the lack of availability, leading people to go online when regular stores were inaccessible. Companies that were able to maintain a steady supply of products to customers emerged as the winners during this challenging period.
Not to mention, the intricate nature of the supply chain also introduces the potential for errors. If the different puzzle pieces aren’t placed effectively, the entire process can slow down, resulting in higher costs. According to Interos’ Annual Global Supply Chain Report from spring 2021, surveyed organizations on average experience a yearly loss of $184 million due to global supply chain disruptions.
Therefore, it is crucial to recognize the inherent vulnerability of supply chains, as they wield significant influence over a business’s cost structure and revenue generation. “So how can we build supply chain resilience for cost optimization?” Building supply chain resilience requires recognizing that there isn’t a universal solution. While there are similarities in how companies handle procurement, production, and distribution, the approach is unique to each. Some companies thrive with a streamlined system, while others value the adaptability of an agile supply management method.
Many businesses find themselves somewhere in the middle, benefiting from a hybrid strategy that combines elements of both lean and agile approaches. To determine the best fit for your company, it’s crucial to understand these options and assess your specific needs.
What is a Lean Supply Chain & Is it for your Business?
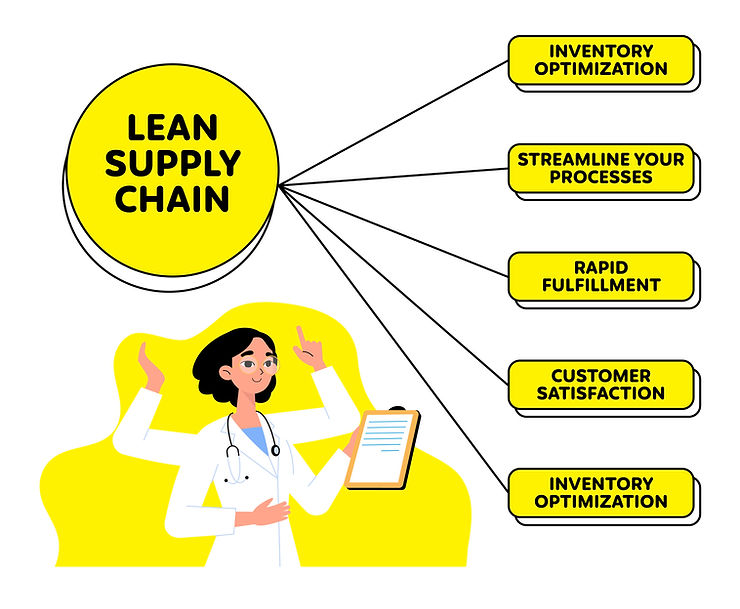
A lean supply chain operates at its peak efficiency, delivering products to customers with minimal waste and adaptability to unforeseen delays. It involves optimizing processes, eliminating unnecessary costs, and reducing storage periods for products.
A lean supply chain offers various advantages. It boosts profits by reducing costs, cuts waste through better resource use, and improves manufacturing quality. It facilitates faster upgrades, streamlines processes, and enhances customer satisfaction with quicker deliveries. In the end, it drives profitability and customer loyalty.
A good case study example of a resilient lean supply chain is Toyota. By strategically sizing inventories, factoring in safety stock, and redefining lead times based on insights from the 2011 Tōhoku earthquake and tsunami, Toyota ensures adaptability. This approach extends to just-in-time manufacturing and tailoring inventory quantities to meet changing conditions along the assembly line. This showcases that lean supply chains aren’t solely about minimizing costs; they’re about strategic optimization, resulting in a resilient and adaptable supply chain capable of navigating unforeseen disruptions.
What is an Agile Supply Chain & Is it for your Business?
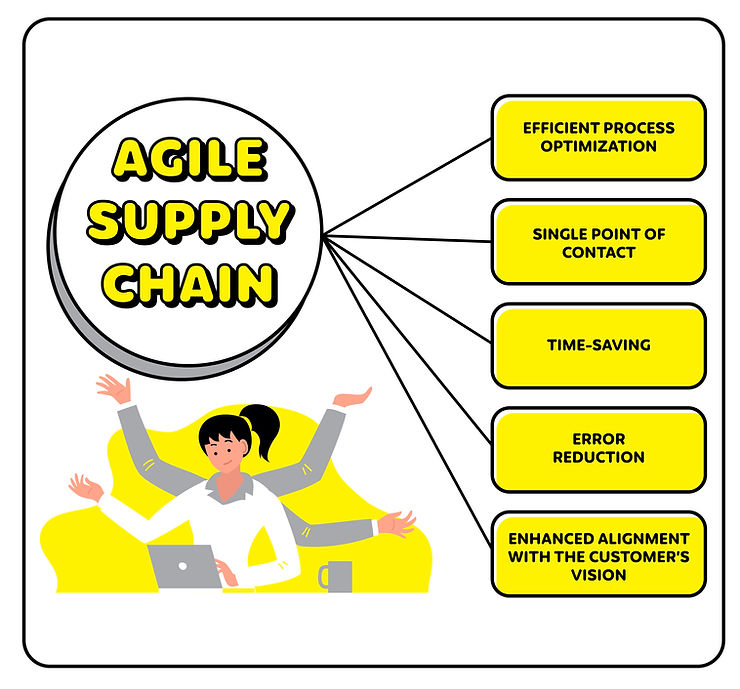
An agile supply chain is characterized by effective collaboration and communication among stakeholders, real-time visibility and data-driven decision-making, streamlined processes, and the ability to quickly adjust production, inventory, and distribution. The goal of an agile supply chain is to enhance customer satisfaction, optimize operational performance, and effectively navigate uncertainties in the business environment.
Over 90% of large companies have encountered a disruptive incident involving a third party within the last three years. This highlights the advantages of streamlining processes, particularly in the context of working with an all-in-one designer and manufacturer. By consolidating the design and manufacturing functions under a single provider, companies can minimize their reliance on multiple third-party entities, reducing the risk of disruptions and enhancing overall operational stability.
Is there a Third Option?
By combining the benefits of various supply chain strategies, a third option emerges: the hybrid approach. While a lean methodology ensures efficiency and cost-effectiveness, it might struggle to swiftly adapt to new demands. On the other hand, an agile approach provides adaptability but can become challenging to manage. The hybrid approach bridges this gap, allowing tailored solutions. Many experts advocate it as the ideal choice for most companies, enabling them to preserve agility while removing unnecessary complexities.
This hybrid approach finds real-world application in companies like Benetton and Kimberly-Clark. For instance, Benetton employs lean principles to forecast garment demand while integrating consumer-responsive elements from agility, ensuring they remain responsive to customers. Similarly, Kimberly Clark leverages lean strategies for consistent product demand and agile techniques for new product introductions to achieve flexibility without compromising efficiency.
Considering the value of a customized supply chain, partnering with an all-in-one product designer and manufacturing supplier can help tailor supply chain strategies to match your unique business needs. In doing so, they optimize operations and ensure your supply chain is perfectly aligned with your unique objectives.
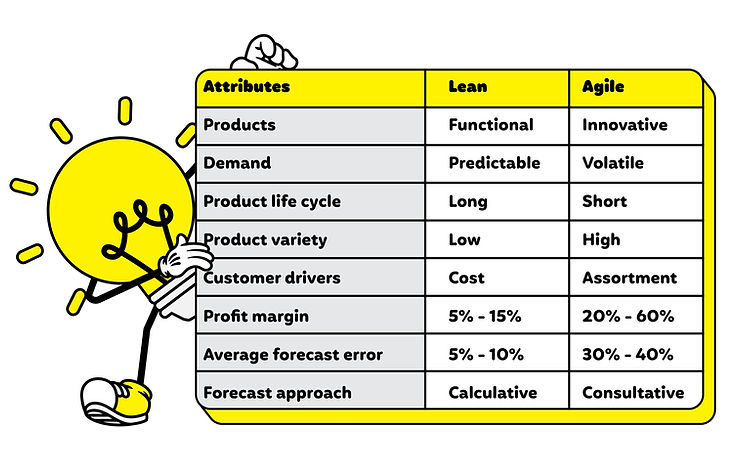
All-In-One Partner and Cost Optimization?
According to a report by the National Association of Manufacturers (NAM), outsourcing production to multiple suppliers can result in increased costs due to additional transportation and coordination expenses. Working with a single provider often leads to more efficient and cost-effective production.
Furthermore, Gartner’s research shows that traditional supply chain cost management models prioritize short-term goals and lack a broad strategic focus. This hinders the pursuit of significant changes and optimal performance. However, adopting an all-in-one solution lowers costs and enables the prioritization of long-term goals, streamlining supply chain management complexities and optimizing costs effectively.
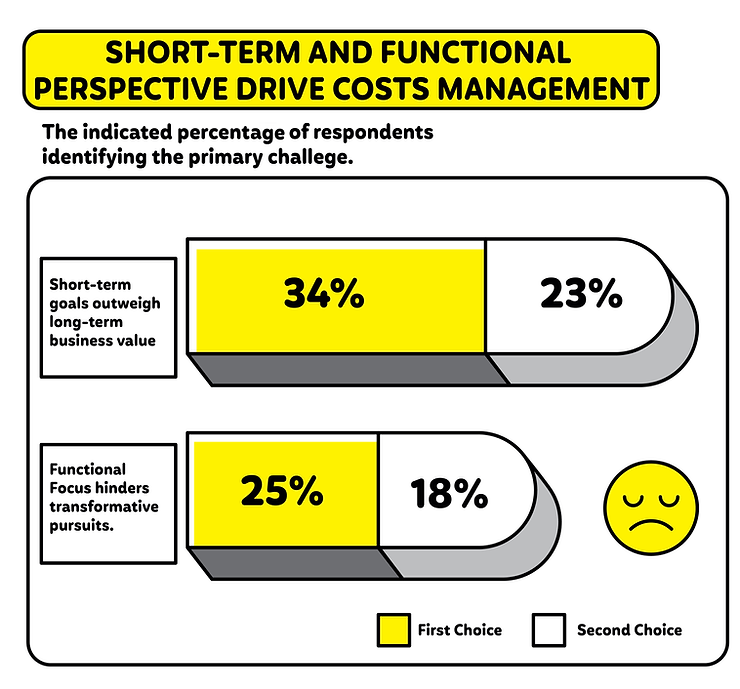
- Efficient resource utilization: Combining design and manufacturing functions enables more efficient use of resources and economies of scale. The all-in-one provider can leverage expertise and production capabilities to optimize costs across the entire process.
- Minimized coordination costs: Consolidating design and manufacturing operations under one roof minimizes costs associated with managing and systematizing different suppliers or subcontractors.
Challenges with Supply Chain and Data Security
Supply chain security challenges are complex, with over 60% of UK businesses receiving fines for data breaches or regulatory violations in the past year. These fines, averaging around £250,000, underscore the financial risks of inadequate security. Insider threats within the supply chain pose a significant danger, as authorized individuals may misuse their access, leading to data breaches or sabotage. Around 20% of survey respondents experienced insider threat incidents in the past year, highlighting the need for strong protection.
Amid these risks, an all-in-one product design and manufacturing partner can play a crucial role in safeguarding data and intellectual property. By providing a comprehensive approach, they ensure that security measures are seamlessly integrated throughout the supply chain. This involves implementing robust controls against insider threats, offering secure data storage, and fostering awareness among partners. By customizing security strategies for your business, such partners enhance protection against cyber incidents, contributing to a resilient and secure supply chain ecosystem.
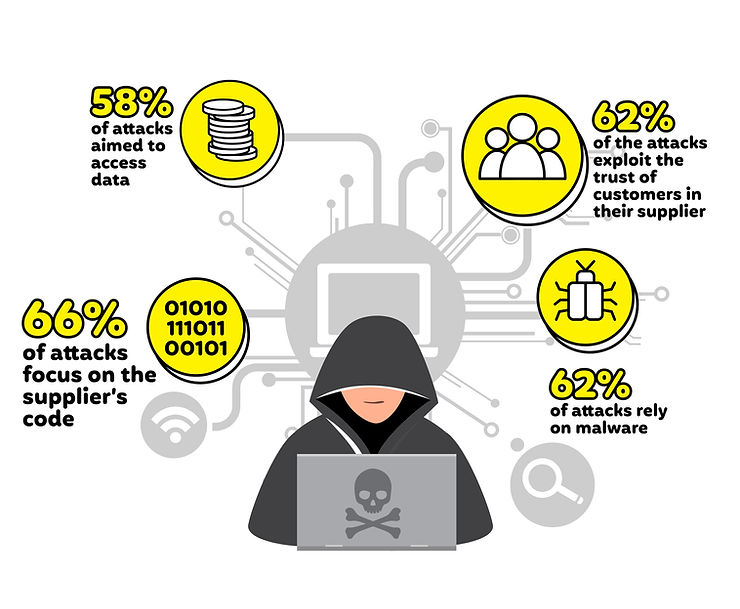
Potential Market for Mass Personalization
On the note of customization, another benefit of working with an all-in-one designer and manufacturer allows for a broader range of customization options. Customers have the flexibility to make changes and adjustments as needed, resulting in unique and tailored products.
Recent market research indicates that approximately 1 in 5 consumers showed a willingness to pay a 20% premium price for customized products. However, when it comes to mass production, 42% of consumers prefer the convenience of being guided by brands and choosing from a curated selection of options. Overall, an average of 36% of consumers in the United States alone have expressed a keen interest in purchasing personalized products, indicating a growing market for personalized offerings.
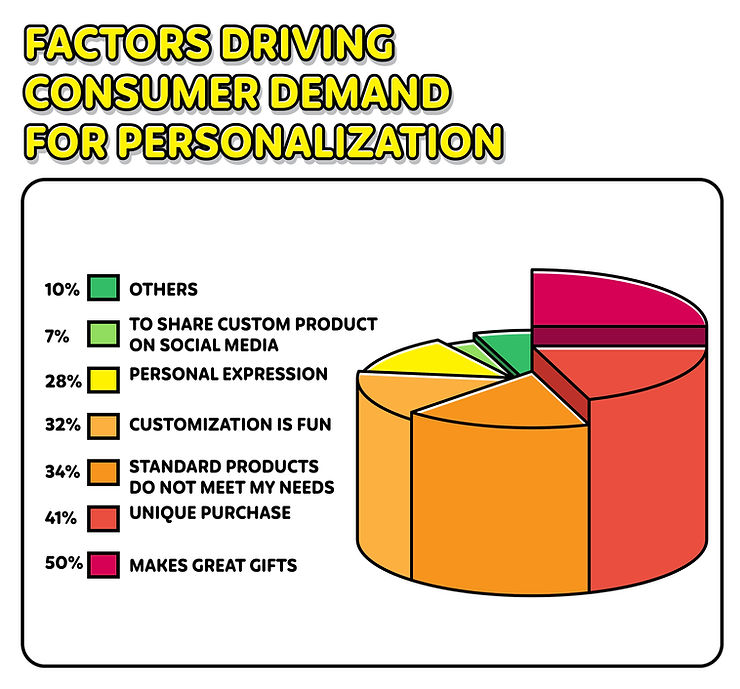
An All-In-One Supply Chain Resilience and Customization
Partnering with an all-in-one provider for product design and manufacturing offers a clear way to address supply chain vulnerabilities and enhance agility. With design and manufacturing expertise housed together, this collaboration not only reduces costs but also streamlines resource use and simplifies coordination. As consumer preferences shift towards personalized products, this partnership empowers businesses to meet these demands effectively. However, it’s crucial to recognize that there’s no universal solution. Success relies on understanding your unique business and adapting your supply chain approach accordingly. The future of supply chains lies in streamlining, resilience, and customization. Having a partner who guides you from idea to creation and customer experience can expedite this journey, ensuring a smooth process in an evolving landscape.